Inspection systems in fully automatic baby diaper making machine use various methods to detect and reject defective diapers before they are packaged. Here are some common inspection systems used in diaper packing machines:
Vision systems
Vision systems use cameras and image processing software to detect defects such as holes, tears, or deformities in the diapers. The system then sends a signal to the control system to reject the defective diaper.
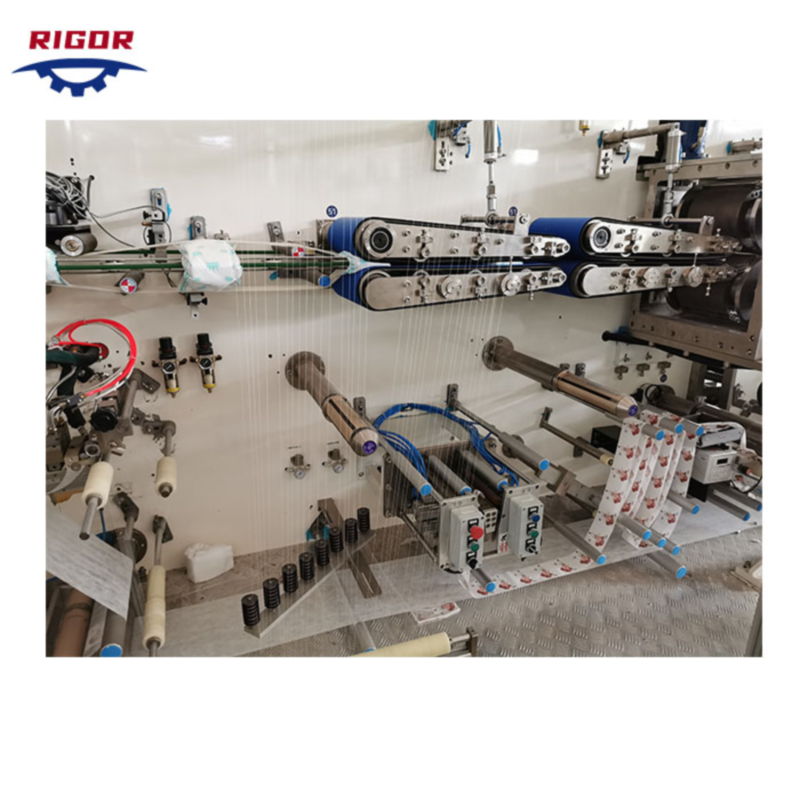
Ultrasonic sensors
Ultrasonic sensors use high-frequency sound waves to detect defects such as missing tabs or poor adhesive bonding. The sensor sends a signal to the control system to reject the defective diaper.
X-ray systems
X-ray systems use radiation to detect defects such as foreign objects or missing components in the diaper. The system then sends a signal to the control system to reject the defective diaper.
Weight sensors
Weight sensors can detect if a diaper is missing any components or if the weight of the diaper is outside the acceptable range. The sensor sends a signal to the control system to reject the defective diaper.
Once a defective diaper is detected, the control system activates a rejection mechanism, such as an air jet or a mechanical arm, to remove the diaper from the production line before it is packaged. The inspection system helps ensure that only high-quality diapers are packaged, reducing waste and improving the overall quality of the product.