Testing 5-way black pipe fittings for resistance to environmental factors such as humidity involves subjecting the fittings to controlled conditions to simulate the effects of high humidity. This testing is essential to ensure that the fittings can withstand environmental conditions without compromising their structural integrity, corrosion resistance, or overall performance.
Here are common methods used to test 5-way black pipe fittings for humidity resistance:
- Humidity Chamber Testing:
- Fittings are placed inside a humidity chamber where the temperature and humidity levels are carefully controlled. The fittings may be exposed to elevated humidity levels for a specified period, simulating conditions similar to those in real-world environments.
- ASTM D1748 Standard Test Method:
- The ASTM D1748 standard test method is commonly used to evaluate the effects of constant high humidity on materials. This method involves placing the fittings in a humidity chamber at a controlled temperature and humidity level for a specified duration. The fittings are then inspected for any changes in appearance, weight, or structural integrity.
- Accelerated Aging Tests:
- Accelerated aging tests may involve subjecting the 5-way black pipe fittings to cycles of temperature and humidity variations. This accelerated testing helps simulate long-term exposure to environmental conditions in a shorter time frame, allowing manufacturers to assess the fittings’ performance over an extended period.
- Salt Spray Testing:
- While primarily used for corrosion resistance, salt spray testing can indirectly assess the impact of humidity on fittings. The test involves exposing the fittings to a salt spray environment, which can accelerate the effects of humidity and evaluate the protective coatings’ performance.
- Visual Inspection:
- Visual inspection is a crucial part of humidity resistance testing. After exposure to high humidity conditions, the fittings are thoroughly examined for any signs of corrosion, discoloration, surface changes, or other visible damage.
- Weight Changes Measurement:
- Weight changes in the fittings before and after humidity exposure can be measured. Absorption of moisture by the fittings may lead to weight gain. Monitoring weight changes is a quantitative measure of the impact of humidity on the fittings.
- Material Property Testing:
- Mechanical properties of the fittings, such as tensile strength, elongation, and impact resistance, 5 way black pipe fitting may be tested before and after exposure to humidity. Any significant changes in these properties can indicate the impact of humidity on the material.
- Electrochemical Impedance Spectroscopy (EIS):
- EIS is an electrochemical technique that can be used to assess the corrosion resistance of materials, including pipe fittings, under humid conditions. It provides insights into the protective properties of coatings and the overall corrosion resistance of the fittings.
- Thermal Cycling Tests:
- Thermal cycling involves subjecting the fittings to alternating cycles of high and low temperatures combined with humidity. This type of testing can simulate the effects of temperature and humidity variations that fittings may experience in outdoor or fluctuating environmental conditions.
- Quality Control Standards:
- Compliance with industry standards and specifications related to humidity resistance is crucial. Following established standards ensures that fittings meet the required performance criteria under specified environmental conditions.
By subjecting 5-way black pipe fittings to these testing methods, manufacturers can assess the fittings’ ability to resist the effects of high humidity. The results of these tests help ensure that the fittings meet quality standards and can withstand environmental conditions, providing durable and reliable performance in various applications.
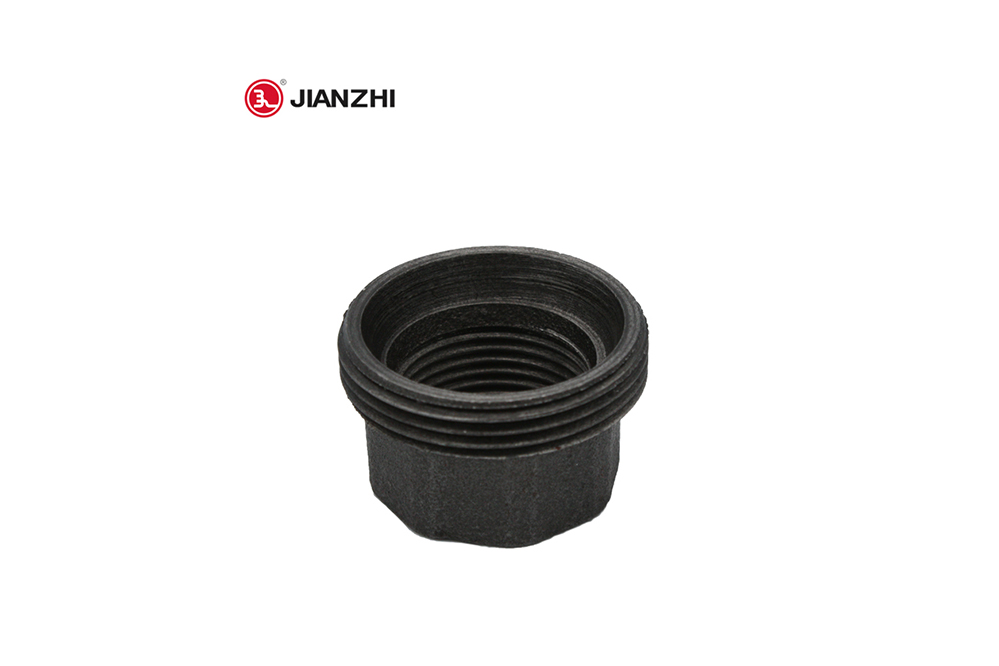